Industry
“Quality is never an accident; it is always the result of high intention, sincere effort, intelligent direction and skillful execution; it represents the wise choice of many alternatives.” William A. Foster.
Over the years much investment has been made in improving the quality of the flour produced at NAMILCO and the efficiency of the mill. This commitment to excellence culminated in 2009 with the achievement of ISO 9001:2008 Quality Management System Certification. The ISO 9001 Certifi-cation has been implemented worldwide, with about one million certificates issued in 170 countries to date. A company’s Quality Management System is comprised of the organisation’s policies, procedures and other internal requirements that ensure customer requirements are met with consistency resulting in customer satisfaction.
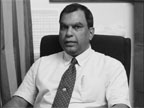
A wise man once said, “There cannot be improvement without new ideas, and there can not be new ideas without the participation of all.”
This is certainly true for the adoption of a Quality Management System by innovative companies such as NAMILCO, where all members of the team are each actively involved as an accountable team member whilst working towards a common goal – QUALITY.
The ISO Certification process began at NAMILCO in 2007, with Delphi Consul-tants of Trinidad being retained to conduct a feasibility study of the milling company’s readiness to qualify for certification. The company was then awarded the contract as consultants to the project in July 2007. The next step was for key staff members within NAMILCO to be given strategic positions and responsibilities within the Quality Management System, followed by preparatory work and the completion of a Pre-Assessment Audit in August 2008.
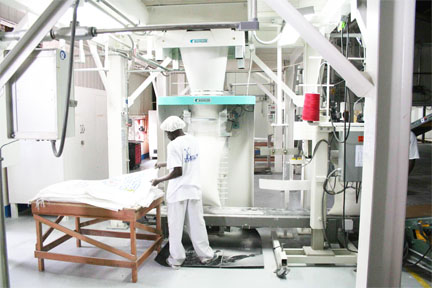
Lastly Société Générale de Surveillance (SGS), an ISO certification body, was contacted to carry out the Certification Audit, Stage 1 of which took place in November 2008.
Société Générale de Surveillance together with its subsidiaries and joint ventures, provide inspection, verification, testing and certification services. With more than 55,000 employees, SGS operates a network of over 1,000 offices and laboratories around the world. Originally founded in 1878 in Rouen, France as French grain shipment inspection house, the Company was registered in Geneva as Société Générale de Surveillance in 1911.
NAMILCO passed the Certification Audit which was concluded in February 2009, resulting in the company being the first in Guyana to achieve this ISO 9001:2008 international standard. National Milling has noted many positive changes in the way the company works as a result of Certification:
Records are now kept in a systematic manner for all processes in the system for future reference, which was not always done in the past. This allow changes to be made more easily and makes it easier to retrieve important information.
Training is a mandatory requirement of the system and everyone is involved. Employees are now aware of their specific functions and the role they must play in helping the company achieve its quality objectives, and this has resulted in a rise in the level of motivation and morale within the staff.
Communication within the organisation is more effective and meetings are held regularly, for example Management Review Meetings, Design and Development Team.
Quality has become everyone’s responsibility and is no longer seen as the function of the quality Control Laboratory alone.
Monitoring of the system is done through regular spot checks and audits are carried out at planned intervals rather than in the haphazard way it was done previously.
Decision-making is not only the domain of top management but is carried out by a collective body that analyse the system’s processes.
Monitoring Customer Satisfaction has become a mandatory process in the system. It is planned and is of great importance to the decision making process.
The achievement of Certification to ISO 9001 also has positive implications for the financial well being of a company. As well as the company running in a more efficient manner, the Certification should result in increased revenues, as other companies prefer to do business with certified companies rather than uncertified ones. Being Internationally recognized, certification also opens doors into new markets, which would also increase revenues.
National Milling Company has provided Guyana with high quality flour products for 40 years. As the country’s only flourmill, NAMILCO produces over 37,000 tonnes of flour per year, which includes close to 10 million small packages of the popular varieties available in the Thunderbolt and Maid Marian Ranges. NAMILCO products have a quality and freshness that offshore competitors cannot match, and with the achievement of ISO 9001: 2008 Quality Management System Certification the company can only go from strength to strength for many decades to come.