President of GAWU, Komal Chand said the new Skeldon factory has an enormous capacity to increase efficiency in the sugar industry but he contended that serious attention was not paid to adequate cane cultivation to coincide with full operations at the estate.
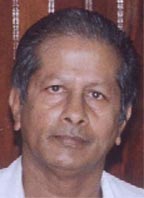
Sugar production at the newly commissioned factory is projected at 116,000 tonnes a year, which Chand referred to as “tremendous output” had the key objectives been achieved. He noted that sufficient cane supply to the Skeldon operation is critical as the local industry struggles to ensure viability in an increasingly difficult environment.
Speaking with Stabroek News on Saturday following the official opening of the factory, the Guyana Agricultural and General Worker’s Union (GAWU) head underscored the need for GuySuCo to boost cane cultivation ahead of its projected 2012 timetable, adding that the period is too protracted.
He said too that with everything set right the factory is expected to considerably lower production cost in the industry where the unit cost of producing sugar remains high.
The expanded operation at Skeldon requires an additional 9,000 hectares of cane lands, according to Chief Executive (CE) of GuySuCo, Errol Hanoman, and around 25 percent of the total cane production for the new factory will be provided by private and corporate farmers. However, cultivation is behind schedule.
Hanoman declared last week at the opening of the factory that intensive work will continue until they reach the full capacity of 1.2M tonnes of cane per annum saying that they are committed to ensuring that the figure is in the ground by December 2011.
But while GuySuCo projects an adequate cane supply in 2012, the President has insisted that cane cultivation be ramped up and results visible as early as 2010. Questions have been raised about the quality of planning that went into boosting cane cultivation to coincide with the commissioning of the factory.
At full capacity Skeldon can process 1.2M tonnes of cane annually or 350 tonnes an hour. The new factory incorporates some of the best technologies in sugar manufacturing and it features a fully automated continuous process, rather than the traditional intermittent batch process.
Other advanced technologies that characterise the new operations at Skeldon include an improved automated punt dumper for offloading cane; a cane shredder to increase extraction; air supported belt conveyors throughout the factory; all electric drives to reduce energy consumption; and self cleaning, single pass, high efficiency boilers.
According to Hanoman the new process enables high thermal efficiencies to be achieved and makes it possible to consistently produce a high quality product. He said too that the technologies at Skeldon are applied to provide a high efficiency manufacturing process that makes the best recovery of the sucrose and the energy in the raw sugar cane.
He explained that the use of diffusion technology, in place of traditional milling extraction, improves sucrose recovery and reduces energy consumption and maintenance costs.
The CE noted that in addition to the expanded cane cultivation, the Skeldon project has delivered two water conservancies with a combined area of some 7,400 hectares and a 12 kilometre-linked canal to provide irrigation and transport services to farmers in the Moleson Creek/Crabwood Creek area. He said also that the large scale expansion of the estate also requires the construction of new infrastructure such as canals, bridges, aqueducts, roads and a major pump station for the recycling and storage of water – all of which are in progress.
He also spoke of the co-generation plant saying that it is an integral part of the operations. Hanoman noted that the plant and the main factory have been fully integrated into a single operating unit and constructed as one project. He noted that the cogeneration factory has the capacity to supply 10 MW of firm power daily to the national grid while producing up to 116,000 tonnes of high quality VHP sugar per year.
Further, he noted that the generation of electricity from the by-product – bagasse will benefit the global environment by the reduction of greenhouse gases, adding that the project has qualified for carbon credits under the World Bank Community Development Carbon Fund. In addition to the environmental benefits, he said, the power capacity will provide an extra revenue stream for the sugar industry.
“This was a brave commitment [by the government]”, Hanoman said while emphasizing that the investment by the administration will boost overall production in the industry to around 435,000 tonnes a year.
Chinese Ambassador to Guyana, Zhang Jungao hailed the factory as the most advanced and largest in the Caribbean region during his brief address. He said that its completion would improve the international competitive ability of industry.
He said that over the past years hundreds of contractors from various Chinese companies were devoted to the project, adding that GuySuCo also put huge resources into project. He recalled that the project encountered countless challenges, citing bad weather, technical issues and transportation problems among others but stressed perseverance. He said too that in the following months Chinese technicians will provide technical support for the operation of the factory.
The estimated cost of the Skeldon project was US$158M in 1998, but a recent estimate is in the region of US$181M, an increase of about 16 percent over eleven years.
There were severe start-up problems at the factory last year. It is now in operation but it is unclear how much cane is available to it on a daily basis.