Caribbean Containers Inc (CCI) is preparing for the distribution of its Eco Pak line of biodegradable food packaging containers in the local market in October and while the manufacturing is being handled by an Asian based company, a feasibility study will be done to ascertain if production is feasible here, Chief Operations Officer Patricia Bacchus says.
Bacchus in a recent interview with Stabroek News declined to name the manufacturing company located in Asia for confidentiality reasons, but noted that CCI hopes to get the sole distributorship for this product line. For the time being the Asian company will be providing the finished product to CCI and the first shipment will arrive by September month end.
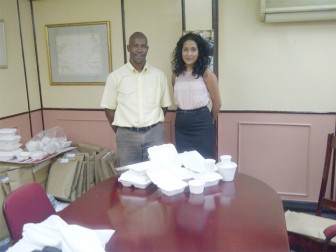
She explained that because this is a new concept it would require extensive feasibility studies in terms of its reception in the local market, an estimation of the quantities that would be required and the availability of the raw materials locally for production.
The feasibility process will take about 12 months to be completed.
The Eco Pak line which is made from bagasse – sugar cane fibre – includes plates and cups and take-out food boxes such as burger boxes and a variety of food and salad containers.
The pricing for the containers has not been announced, but they decompose in 90 days once exposed to a combination of bacteria, soil, oxygen and sunlight. From all the indications many large-scale business entities have responded positively to the initiative which was launched earlier this month.
Government, in a bid to improve the environment had announced in June that it would soon be enacting legislation to ban the importation of non-biodegradable material including styrofoam and plastics, and that it would increase littering penalties.
During the interview held at the company’s Farm East Bank Demerara address, Bacchus said that “[CCI] will be distributing it on the local market getting a feel of the market conditions, the quantity required and similarly we will [eventually] be finalizing the capital investment required to manufacture them here.”
She said that for the line to be economical the items have to be manufactured on a very large scale, and as such CCI is looking to have countries such as Barbados, Trinidad and Tobago and Jamaica on board “before we can go ahead with production locally.”
Bacchus told this newspaper that another factor determining manufacture here would be the availability of sugar cane fibre locally as at present bagasse is going into alternative fuel for boilers, and “there is not a surplus to go into this production so we have to also look at sugar cane cultivation probably in collaboration with another entity.”
Sugar cane, she noted, is the ideal crop for the line although there are a few suggestions about substitutes – straw, bamboo and the traditional wood pulp. She said that the latter would not be an ideal choice for CCI because “we are in the recycling business and our first option is not to use virgin pulp from trees; our first option is using other resources which are easily renewable or reusable.”
Research, Development and Sales Agent Dwayne Scott who was also present at the interview noted that the other concern with trees is the issue of deforestation. He said that re-growing trees would take years while sugar cane is a product that can be re-grown within a year‘s span. “It is totally renewable in comparison with all the other resources that are available,” he added.
Production process
Meanwhile Scott said that the production process for the line of products is very complex. He said that the first step is that the bagasse raw material is ground and pounded to a pulp. This pulp is thrown into a tank, he explained, where it is further liquified and subsequent to this the solution is passed through different machinery where liquids are extracted in order for it to reach the desired consistency.
Thereafter, it is poured into a mould, Scott said, adding that soluble oil is added which helps the product maintain its form. Once the process of moulding, is complete, the product then is shaped and any excess material is trimmed, before undergoing various tests including heat, metal and cold tests – all of which are in keeping with internationally approved standards.
Bacchus added that during the pulping stage/vacuum extraction stage, the product is treated to ensure safety for food use and to remove any contaminants which might have been on the sugar cane crop, adding that other tests including that for mildew are also done.
According to Bacchus each container goes through a very rigorous quality inspection at the production plant which has UV sterilization. She said that each product is tested for thirty minutes with oil at 95 degree Celsius and water at 60 degrees, after which they are each physically checked for deformation, wrinkles and leakage, that are all part of the QA (quality assurance) test.
Additionally she said that the products are made under the strictest hygienic standards. She explained that any staff member entering the plant has to pass through a UV sterilization room. “There is no exposure of hair, hands are always in gloves, [and there is a] face mask,” she said adding that there is a manual quality control which includes testing for colour, odour and ensuring that the surface of each product is smooth, clean, has no wrinkles, no peeling, no ruptures, no perforations, oil, mildew or other foreign matter. Checks are also made to ensure that the edges are smooth and neat and that they facilitate products covered with lids.
Asked if any CCI official has visited the company to see firsthand how the manufacturing takes place, Bacchus replied in the negative. She said that while no visit has been undertaken the company concerned has sent all its ISOs and quality certifications (original copies) as well as extensive photographs of the plant, of their quality assurance procedures and of their inspection procedures. She said that CCI has also received a detailed listing of all raw materials used in the process and all other information as it relates to production.
“We do recognize the need to go up and see them, and we will” she said.
She later added that it will take about three weeks from when the product is ordered and shipped. She made it clear that it does not take three weeks for the products to be manufactured but noted that “They would produce all similar items at the same time. Taking into account planning and scheduling and so on we are looking at three weeks.”
Positive feedback
Bacchus told Stabroek News that since the product launch several weeks ago a number of big companies and organizations, including the US Embassy, had taken an interest.
She described the response as very positive noting that several companies have made contact with CCI expressing an interest in the Eco Pak line. Among them are M &M snackette, JR burgers, New Thriving restaurant, Oasis Café, Jerries, Maggies, Princess Hotel, the Central Islamic Organisation of Guyana (CIOG), and a number of religious organizations.
“It would be easier at first for them, especially if there is a minimal price difference between this and styrofoam. It is easier for them to absorb that without passing it on to their customers,” she said.
Scott said that CCI has been looking at a number of models around the world, a good example had been the approach of London for the 2012 Olympics for which a full regime of packaging solutions was created.
Bacchus added that at present her company is engaging the government on adopting the line of products and using it at all government sponsored events.
She said that the introduction of this product is in keeping with the Low Carbon Development Strategy of the country and “we would only encourage other entities to find more sustainable products that they can use in their operations.”
While expressing the view that Guyana is ready to take this approach which has already been adopted by developed countries, Bacchus said that its success here is largely dependent on the reception from the business community.
She said that no one had proposed partnering with CCI to enter into production with it. According to Bacchus the Bag Bay women – who are bringing paper bags as an alternative to plastics – have already indicated they wanted to move the Eco Pak line into the local market.
Scott meanwhile expressed the hope that the introduction of this product will create “a total shift in the Guyana market from the non-biodegradable products to a more sustainable product. It is a good move for Guyana since most Caribbean countries use paper based products and I think we are the first to go fully biodegradable, and I think it is an excellent venture for Guyana and our company.”
Giving some background information on CCI, Bacchus said that it all started in 1983 with a package plant right at Farm where corrugated packaging was produced. In 2003, CCI, she said unveiled its paper recycling plant which recycles old cardboard.
Prior to 2003, she said all the paper used to manufacture the boxes was imported and it was virgin paper from wood pulp. Now with the recycling mill, CCI recycles old boxes with 90% of the corrugated packaging using the recycled paper while the remainder uses imported material because it is for special requests such as pizza boxes.
Bacchus described the company as a publicly traded company which commenced a restructuring programme from January 1, 2007 under new ownership, and since then the growth trend has been extremely positive. At the end of 2006, she said the company was actually facing foreclosure. From January 2007 when the restructuring commenced to December 2011 the company has come into a cash positive position, Bacchus said, adding that from December 2011 to date there has been profitability. “So it has been a remarkable five year turn around for us,” she said.