Australian company Pharsalus Gold Inc has applied to the environmental authorities for an authorisation for large scale gold mining at Black Water Creek, Kaburi Area, in Region Seven, which will use cyanide in its recovery operations and an impact assessment now has to be done.
A notice posted by the Environmental Protection Agency (EPA) in yesterday’s newspapers said that Pharsalus Gold Inc
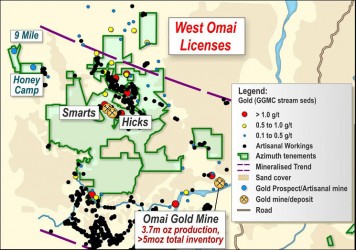
is planning mining within the Hicks/Kaburi Concession and that an Environmental Impact Assessment (EIA) is required for this project since it may have significant impacts on the environment.
Planned use of cyanide will raise environmental concerns as it recalls the biggest environmental disaster to hit the country—the 1995 collapse of a tailings pond at Omai Gold Mines Limited used to store cyanide-laced effluent.
The EPA notice said that the project would entail an open pit mine which would see the clearing of vegetation, stripping of topsoil and blasting of hard rock. The project also encompasses construction of a processing facility, laboratory, cyanidation facility, power generating facilities and ground water wells. It would also require the upgrading of an existing access road.
Pharsalus, a wholly-owned subsidiary of Azimuth Resources Limited, has been prospecting here for a number of years. One of its sister companies has also been interested in exploring for rare earth metals here.
According to the project summary, the mine will be focused on the recovery of ore for processing from the Smarts and Hicks gold deposits, which is part of a 1,100 km2 area the company acquired by vendor agreements and direct grants.
The development and operation of the mine site, it added, will involve several distinct phases, including the construction of the mine site infrastructure and upgrade of the mine site access road, construction of a process plant, staged construction of tailings pond, and construction of a raw water dam.
Saprolite
It said exploration work at the mine site has established the presence of viable grades of ore in the area identified for the open pit mine, with maximum dimensions of 1,500m in length by 350m in width and approximately 180-240m deep. It noted that saprolite ore—a chemically weathered rock—represents less than 10% of the total ore and is positioned in approximately the upper 70 metres of the pit. The remaining fresh ore, it added, is primarily massive intermediate volcanics with chalcopyrite and gold mineralisation. “The saprolite ore, low in sulphides, may be amenable to gravity concentration and may not need to be treated with a cyanide leaching process for gold recovery. This aspect is currently being investigated in metallurgical testing,” it said.
The company is assuring that the project will be designed and operated in accordance with environmental protection requirements and guidelines. As an example, it said the project footprint and land clearing limits will be monitored and controlled over the life of the project. The footprint design will aim to reduce disturbance to forested areas.
Mining and processing is projected take place 24 hours per day, 7 days per week and 365 days per year. It said conventional truck, shovel and wheel loader surface mining methods will be used in the open pit operations and materials to be mined will be sampled at the face to determine whether they are waste or ore, and the boundary between the materials marked by flags and pickets before their excavation. “It is expected that an ore stockpile would be maintained at the processing plant to provide up to 5-7 days of run-of-mine ore storage capacity. Low grade material that would otherwise be disposed as waste rock will be temporarily stockpiled and reclaimed and processed after the pit is mined-out,” it said, while adding that the ultimate limits of the open pit will be defined by the open pit design, which is being developed.
According to the summary, the mine pit will be developed in “phases” or “push-backs.” It explained that the saprolite will be stripped and either processed, stockpiled for processing or disposed in the waste dump if of inadequate grade, while the hard rock will be mined after enough saprolite ore has been mined to provide adequate working faces for the hard rock mining to begin. “Each phase will be mined to ensure that safety, working area requirements, mine access and service requirements are taken into consideration,” it noted.
Fifteen years
The summary further said that mineral processing will consist of handling the saprolite ore and fresh ore by blending the two together and processing singularly. “The softness and clay content will make processing of the saprolite more challenging with conventional conveyance method. The saprolite ore would therefore be blended at a very low rate to address the potential material handling problems,” it explained, while adding that the ore exploitation rate will result in a mine life of 15 years or more depending on the final processing rate.
The project summary explained that the processing plant will consist of the following process stages: single-stage crushing; stockpile reclaim, single-stage milling and classification; gravity concentration and intensive leach recovery; CIL leaching and gold recovery via carbon elution; and cyanide detoxification and tailings storage.
The plant is to have a nominal capacity of an estimated 600,000 to 750,000 tonnes of ore per annum, designed to produce up to 110,000 ounces of gold per annum based on an average overall recovery of 92%.
Further, it said the plant Run of Mill (ROM) pad and primary crusher will be located on a ridge approximately 650m southwest of the Smarts pit in order to avoid fly-rock and will be close enough to minimise mine haulage costs. The remainder of the treatment plant will be approximately 800m from the mining operations along the same ridge as the ROM pad.
The summary added that mill feed ore will be introduced into the treatment plant from a 3,000 tonne-live capacity open air stockpile at a design rate of 94 tonnes per hour. The treatment plant is projected to operate 24 hours per day, 365 days per year at a nominal availability of 91.3% for a total of 8,000 operating hours per year.
The construction of the ore processing facilities is expected to take nine months and it is planned that the development of the open pit will be timed so that the pit can begin to supply ore to the processing facility once it is constructed. The summary also said that the Tailings Storage Facility (TSF) will be located approximately 600 meters to the south of the process plant and will be a valley storage facility with the containment embankment at the eastern end of the valley. “The TSF will be constructed in a staged fashion with stage 1 being sufficient to store 2 years volume of process tails and rainfall runoff,” it noted.
In addition, the mine site is be serviced by road and air. According to the summary, a new access road will be constructed to connect the mine site to the Amaila Falls Hydropower service road. The access road will be 9m wide and approximately 8km length and will consist of two 3.5m carriageways plus 1m shoulders as well as associated drainage ditches alongside the road, it said, while detailing that a 1km section of road will be constructed to provide access from the site access road to the proposed airstrip. That road will be 6m wide and will consist of two 3m carriageways, plus associated drainage ditches alongside the road. The airstrip will be located about 1.4km south of the process plant and will be designed to carry the Cessna Caravan which is a class B1 to B2 aircraft, the summary noted.
Meanwhile, members of the public have 28 days from yesterday’s notice to make written submissions to the agency setting out questions and matters which they require to be answered or considered in the EIA.
The EPA notice said that a summary of the project is available on the EPA website (www.epaguyana.org) or can be uplifted for a reasonable cost for photocopying from the office of the Director of EPA’s Environmental Management Permitting Division, at Ganges Street, Sophia, Georgetown.