The crash of a Cessna 208B Grand Caravan aircraft while on a shuttle from Olive Creek to Imbaimadai on January 18, 2014, which caused the deaths of Canadian pilot Captain Blake Slater and Guyanese cargo handler Dwayne Jacobs has officially been deemed the likely result of engine failure.
Investigations conducted by the Guyana Civil Aviation Authority (GCAA) with support from the Transport Safety Board (TSB) of Canada and the National Transport Safety Board (NTSB) of USA and the aircraft engine manufacturer, Pratt & Whitney Corp (P&WC), Canada concluded that “the probable cause of the accident was due to a power loss suffered by the engine.”
“The power loss was associated with the fracture of one of the 1st stage compressor stator vanes by fatigue,” the comprehensive investigators’ report said.
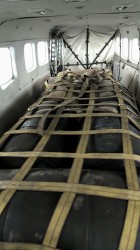
On Friday, Trans Guy-ana Airways (TGA), the domestic airline which operated the flight stressed in a press release that the report had not found it in any way culpable for the crash, as the power loss was found to be “a result of the engine manufacturer’s fault and not from any maintenance oversight on the part of the maintenance provider nor from pilot error.”
According to the report, “The fatigue crack originated from a lack of brazing adhesion extending over approximately 0.280 inches along the chord length and 0.050 inches in the direction of the shroud thickness and was located between the leading edge and mid-chord of the vane,”
This finding, according to TGA, was determined when the engine was stripped and examined by the engine manufacturer, under the supervision of the NTSB. “It was determined that the engine lost power as a result of the engine manufacturer’s fault and not from any maintenance oversight on the part of the maintenance provider nor from pilot error,” the release said.
Despite this declaration, TGA has since taken steps, in line with several other findings, to cushion the impact of any crash of its cargo flights on those aboard.
One such step is the creation of possible forced landing sites which “have been identified along the shuttle routes and programed in the GPSs for easy access in the case of emergencies.”
TGA has also replaced all tie down with more sturdy ones that provide enhanced crash load restraint and a flight operations officer is stationed at interior locations to prepare the relevant documentations for each flight while ramp attendants have also been trained at all locations in aircraft loading, tie down procedures and general ramp safety procedures and the aircraft loader’s seat, has been changed from behind the pilot to the co-pilot’s seat.
TGA has further noted that it has since upgraded its spot tracking devices to spot every two and a half minutes instead of every ten minutes.
“It is the policy of TGA that the Safety Manage-ment System function to ensure compliance with established systems and procedures as detailed in our Operations Manual and to ensure that the standards are maintained by all departments on a continuous basis,” said the airline.
TGA said it has implemented a continuous monitoring approach to ensure that areas of non-conformity are addressed in a timely and suitable manner to ensure continuity of standards and the corrective action must be such to prevent the recurrence.