The partnership between Guyanese manufacturer DuraVilla and Barbados’ National Housing Corporation (NHC) is set to have spinoff effects for businesses here as well as on the island, the company’s Chief Executive Officer Rafeek Khan says.
The local company, which specialises in pre-fabricated homes and hardwood products, recently secured the opportunity from the Barbadian government to provide 1,000 prefabricated homes as the island aims to provide housing solutions to low income families.
The company will be constructing 600 square-ft two-bedroom houses, outfitted with photovoltaic energy generating panels. They would be valued at 100,000 Barbados dollars.
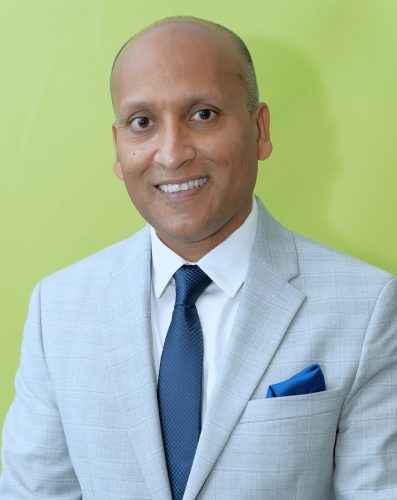
During the island’s Agrofest exhibition, held at the Queens Park last month, Barbadian Minister of Housing and Lands Dwight Sutherland had said that the first set of homes are scheduled to arrive on the island by August.
Speaking with this publication on the initiative, Khan said the company has modified the design of homes to meet the requirements of the Barbados people and ensure they are safe and suitable for even during hurricane season.
The homes have been retrofitted to feature higher pitched roofs, shorter overhangs, tied columns and other technical elements to ensure they are grounded in the event of a storm. From the NHC front, the homes will be equipped and mainly powered by photovoltaic (solar) power panels.
“We have taken timber and designed it to have a very appealing element. We wanted to have a home that has the necessary amenities and very modern outlook. No matter which level you are entering this home ownership from, this home should be comfortable, affordable and appealing for all,” Khan explained.
He highlighted that while wood species such as green and purple heart have worked in the past for such projects, his company has been able to work with Wallaba.
“It has been a test of time for us because it is not an easy wood to work with but we have been able to treat it and work with it. Also it is less expensive than green heart and purple heart,” he added.
Under the deal, DuraVilla will begin shipping homes within 90 days. The full complement of homes are expected to be delivered within a 12-month period.
“We are looking at shipping roughly about 30 a month and we can ramp up. We are looking that by August we should have these homes going up across Barbados…. once Mr Khan puts together the order from us, we should have some homes going up by August, worst case September,” Babados Today reported Sutherland as saying earlier this month.
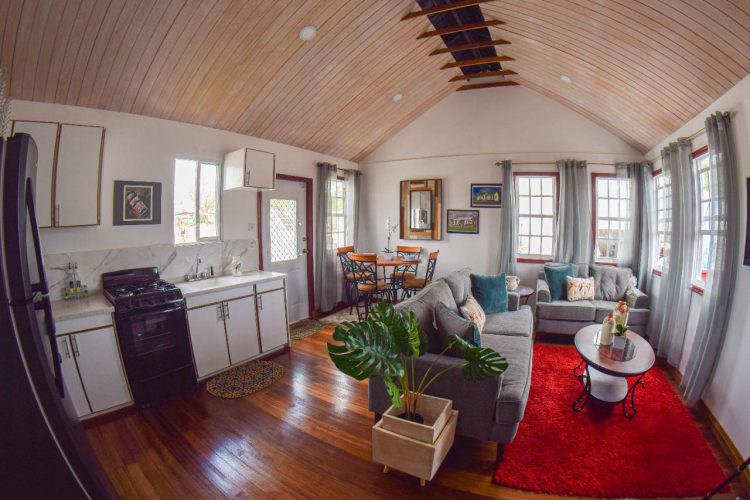
Khan explained that the company has been building its inventory to cater to the demand. He noted that while they have cured and dressed wood on hand which can be used, it will set back orders for other markets. He nonetheless noted that with processes from harvesting to manufacturing taking over a month, once the inventory is built up they will be able to increase the number of units they can ship at a time. They will first start with 30 units and then look to ramp production in the ensuing months.
The CEO stressed that as demand grows the company will also have to expand its workforce and supply chain. This is where he said the deal will yield spin off effects. He stated that while they are going to need people to work on the processing and manufacturing lines here, they will utilise the skills of Barbadians for finishes.
Transferring skills
Guyanese who participated in helping to assemble the home for the expo, Khan said, were exposed to techniques in finishing to make the homes more appealing. In light of that, he stated that they will also be looking at having some skill transfer to Guyanese.
“It is important we prepare and develop our skills in finishing. The Barbadians are good at that, they have excellent skills in finishes from working in the hotel and tourism industry. They know techniques in painting and trowel texture plastering and other areas. So we want to benefit from skill transfer between the two countries,” he explained.
When the homes are shipped and assembled on the island, the workers in Barbados will be responsible for electrical and plumbing installations as well as that of security features, such as metal shutters, louvers and burglary prevention bars.
Khan also pointed out that while a product might function well on the home for Guyana’s climate, it might not be appropriate for Barbados’ conditions. This is where, he added the Barbadian suppliers will play a major role since they are aware of the needs of the housing sector.
“It is not feasible that we ship materials like tiles, bathroom fixtures and locks and windows among others here and then ship it back to Barbados. The suppliers there are aware of the standards and building codes, so we will utilise that route,” Khan noted.
Sutherland was quoted in the Barbados Today as saying “We are utilising local building material – the roofing that is local Permaclad, concrete board. We are using Fiberpol to install our sinks. We want to thank UNICOMER for the display, and BNOC [Barbados National Oil Company] came and they installed the photovoltaic panels. Most of the other materials will be locally made and we will utilise locals to fully outfit.”
Khan stated that the houses will be assembled in such a way to cater for expanding from two-bedrooms to three or even cater for a patio.
The DuraVilla CEO stressed that the time in Barbados during Agrofest was beneficial as they were able to learn a great deal from customers about their likes and dislikes.
He noted that the house was well received and many viewed it as a meeting of luxury, modern design and affordability.
Additionally, Khan said the partnership will significantly increase the contribution of forestry to the country’s GDP per annum. Currently, he stated, the sector contributes 3% of the GPD.
He stated, too, that they will be able to increase employment in the sector by 2,500 jobs and increase export earnings for timber alone by 25% in the first year.
When asked if the ramp up in production will not have an impact on Guyana’s deforestation, Khan responded in the negative and stated that the country is currently not harvesting to its allowable quota for sustainability. Guyana, he noted is allowed to cut a maximum of a million cubic meters per annum but is currently harvesting a third of that.