3D printing could soon be the new norm in the construction of local homes, saving builders time and money while offering higher quality, according to the Chief Executive Officer (CEO) of Black Buffalo 3D, Michael Woods.
“This is a real credible technology now that is overtaking many of the traditional ways of doing construction,” Woods told Stabroek News in an interview at International Building Expo on Friday.
The New York-based Black Buffalo 3D is one of the prime exhibitors at the ongoing International Building Expo at the Guyana National Stadium at Providence. Over the course of the three-day event, it will utilise its commercial-grade 3D printer to build a 600-square ft home–the first 3D printed house to be created here.
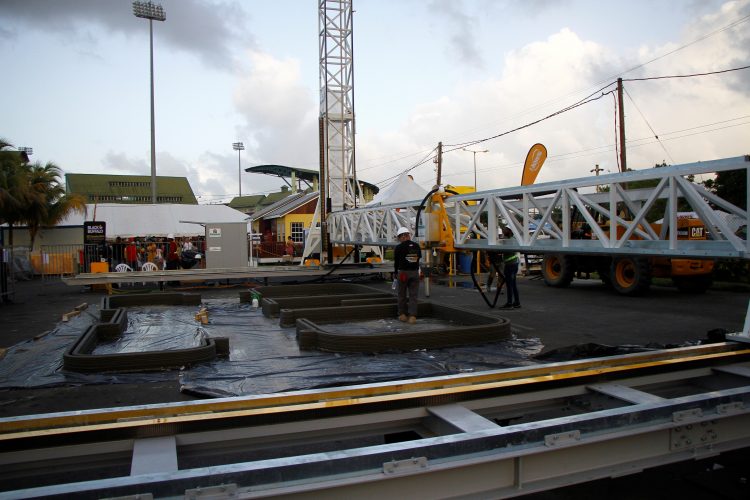
Woods said the Black Buffalo 3D printer is designed to provide contractors with the technology and materials to save time and money.
“We can build a 1,000 square-ft home, 9-ft-high walls in roughly 20 to 24 hours depending on how many inside and outside walls you have,” he explained.
Black Buffalo 3D is committed to improving construction sustainability through waste reduction and lowering environmental impact and the overall greenhouse gas emission from concrete.
Therefore, instead of stones, Woods explained, silicon sand is being used. “We are using very fine granular sand…not stones……So we are decreasing the carbon footprint of the concrete…And concrete is 8% of all global greenhouse gas emissions,” he said.
In addition to the time and costs saved with 3D printing, Woods said a printed house is three times stronger than those built traditionally. “The quality of this is three times as strong as CMU (concrete masonry unit) blocks. CMU blocks are usually between 2800 and 3500 pounds per square inch. We cure over 10,100 pounds per square inch,” he explained.
Additionally, the printer has more architectural ability. “You can do circles and you can also do hard corners. When you have block, all you can do is a hard corner. So you have so much more architectural ability to be able to customize your home and make the home yours,” Woods said.
Windows and doors are not printed and therefore the process would still require a human workforce.
As a result, Woods told Stabroek News, over the past two weeks approximately 10 to 15 Guyanese were trained by Black Buffalo 3D.
All materials for the printer are sourced here, Woods also assured.
Aside from the high demand in the housing sector, Woods said Black Buffalo 3D also eyes printing highways, culverts, drains and seawalls in the future.
According to Woods, the goal is to have a 3D printer at every construction site across the country. “It’s not if, it’s when that happens. This is so much faster, so much stronger, so much less expensive and so much more flexible and the ability to make design for the house,” he said.